Finished Business
Well-Known Member
Got a few more odds and ends done on the boat. Finally finishing the floor up so that it is ready for install. The final step was to install an access hatch to get at the tank switches, that allow me to switch between my main and reserve tank.
Reviewing my options in hatches, I decided to go with a round 6" hatch with a clear plastic cover. Its fairly low profile, so the 'tripping-over' factor will be minimal. I wanted to go with the clear when I saw it because it makes for very easy viewing of which tank I am running off. Just one more piece to my fool-proof fuel system.
After that it was time to get the floor sandblasted with Starblast (small ball-shot) media to give some added grip and texture...it leaves the surface of the floor similar to a fine sand paper. It may pick up dirt, but it will be slip-proof for the life of the boat, its a fishing machine, not a day cruiser so I'm not worried. I had an idea that I thought would be cool. If I could mask parts of the metal using PVC tape, I could have some bare metal still exposed in areas where the grittyness of the sandblasted floor would be troublesome. I designed the mask areas in a way so that dirt and filth would have smooth 'channels' so-to-speak that the water would flow off and towards the stern of the boat. As well I masked the area infront of the cuddy door, and at the rear where most water will be bailing into the bilge, to limit green growth and dirt build up in the areas that would be better left clean. Its a nice custom touch I'm pretty happy about and it should make it all the more fish-worthy.
I considered having a design printed and masked to the floor, but beyond straight lines it became a lesson in frustration more than anything. The blaster should have the material for a few days and then I can get it back and get on with the final floor installation.
I had mentioned using something to dampen vibration between the floor and the stringers previously. The blaster had a great recommendation...using a 40mm PVC tape to stick onto the stringers. Its a 40 year rubberized product that I think will more than do the job. Add a little sikaflex and it should be a rock solid floor!! heres a few pics of what I've just described...happy to be posting again, I HATE when this thread gets to Page2, its a blatant sign I'm being lazy!
Cheers!
Nick-FB
Reviewing my options in hatches, I decided to go with a round 6" hatch with a clear plastic cover. Its fairly low profile, so the 'tripping-over' factor will be minimal. I wanted to go with the clear when I saw it because it makes for very easy viewing of which tank I am running off. Just one more piece to my fool-proof fuel system.
After that it was time to get the floor sandblasted with Starblast (small ball-shot) media to give some added grip and texture...it leaves the surface of the floor similar to a fine sand paper. It may pick up dirt, but it will be slip-proof for the life of the boat, its a fishing machine, not a day cruiser so I'm not worried. I had an idea that I thought would be cool. If I could mask parts of the metal using PVC tape, I could have some bare metal still exposed in areas where the grittyness of the sandblasted floor would be troublesome. I designed the mask areas in a way so that dirt and filth would have smooth 'channels' so-to-speak that the water would flow off and towards the stern of the boat. As well I masked the area infront of the cuddy door, and at the rear where most water will be bailing into the bilge, to limit green growth and dirt build up in the areas that would be better left clean. Its a nice custom touch I'm pretty happy about and it should make it all the more fish-worthy.
I considered having a design printed and masked to the floor, but beyond straight lines it became a lesson in frustration more than anything. The blaster should have the material for a few days and then I can get it back and get on with the final floor installation.
I had mentioned using something to dampen vibration between the floor and the stringers previously. The blaster had a great recommendation...using a 40mm PVC tape to stick onto the stringers. Its a 40 year rubberized product that I think will more than do the job. Add a little sikaflex and it should be a rock solid floor!! heres a few pics of what I've just described...happy to be posting again, I HATE when this thread gets to Page2, its a blatant sign I'm being lazy!
Cheers!
Nick-FB
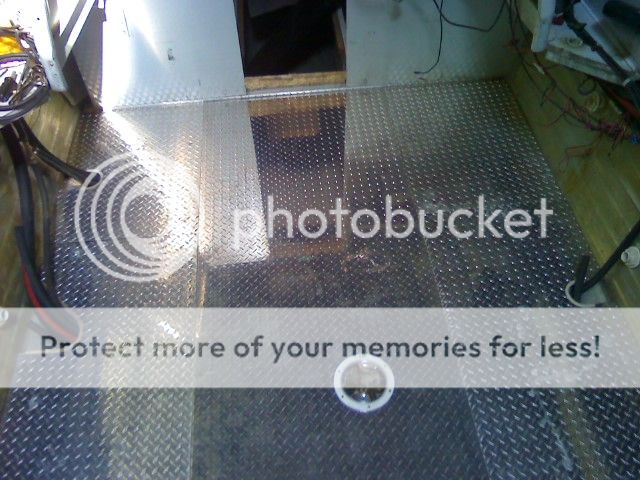
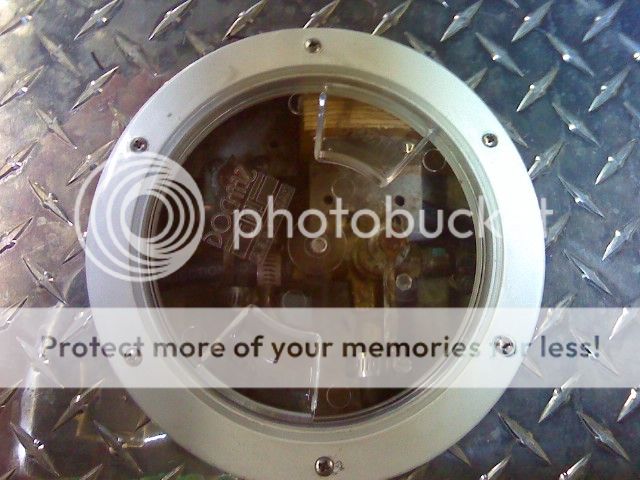
